Getting trains back on track
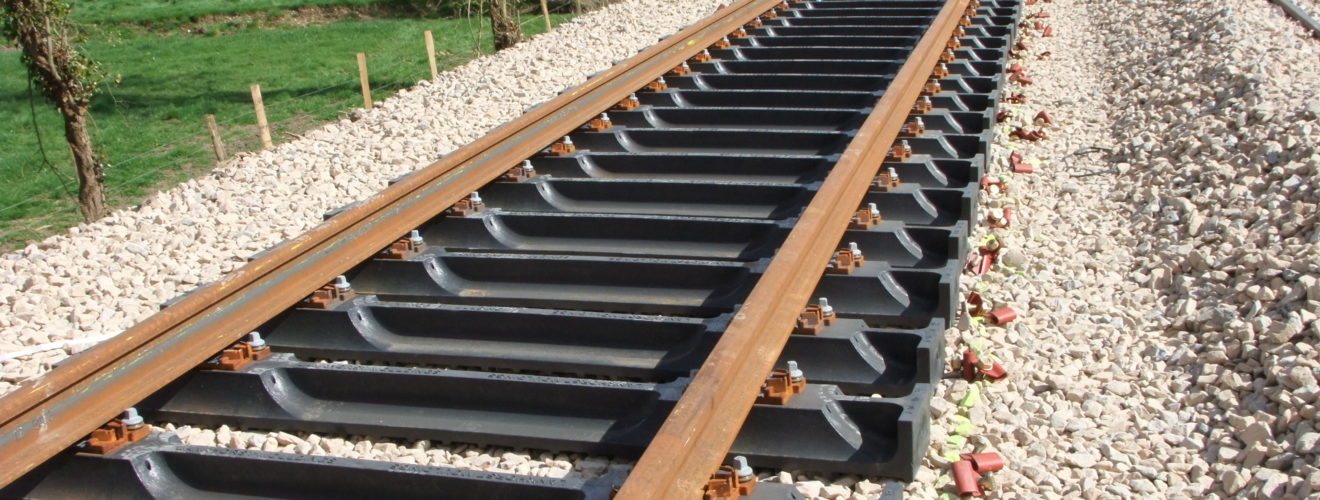
Train delays are at best irritating, and at worst a nightmare. This is certainly the grievance shared by the thousands of tweets marked with the hashtag “#scotfail”. There are many reasons a train service may be delayed, including broken or damaged tracks. Imagine then, the advantage of a system which could locate track defects before they worsen and eventually break.
Mounting accelerometers on trains would allow continual vibration measurements; sudden changes in vibration could then signal a defect in the track. Low frequency vibrations suggest bends or deformations, while high frequency vibrations suggest corrugation – a bumpy surface – along the track.1 Defects like this worsen over time until they eventually become bad enough to make a track unusable. Being able to diagnose defects early-on equips engineers with the information to schedule repairs at more suitable times, rather than having to cancel trains when the deformations unexpectedly make tracks unusable.
The typical equipment for measuring vibrations are piezoelectric accelerometers (piezoelectric is a type of electricity, generated in response to applied mechanical stress). However, these are not ideal as their measurements are distorted by electromagnetic interference (EMI), which is abundant along train tracks.2 Housing the accelerometer in an insulating material becomes necessary to prevent EMI influence. The addition of the insulating material makes the total cost of accelerometers very expensive.
Accelerometers based on optical fibres have been suggested as an alternative as they are not affected by such interference. Researchers from The Hong Kong Polytechnic University have proposed a particularly promising fibre accelerometer which is based on an effect called birefringence. In most fibre optics applications, birefringence is something to be avoided. However, these researchers have decided to use it to their advantage: they have designed optical fibres which encourage birefringence such that the change of the light travelling through the fibre is proportional to the vibration experienced, therefore allowing measurements of vibrations.3
Birefringence is seen when a signal traveling along an optical fibre is distorted by some external influence such as pressure, vibration or bending of the fibre.4 In this group’s work, the sensor was put to the test when it was mounted on an operating train. An industry standard piezoelectric accelerometer was also mounted on the same train for comparison. The train travelled 1.75 km, a distance which included a crack on the rail track. The new sensor displayed operation comparable to the piezoelectric accelerometer, and successfully identified the crack on the track. These promising results suggest that this new technique could provide the key to continual monitoring of tracks.5
With the ability to predict and prepare for breaks on train tracks, the frustrating wait for delayed and cancelled trains could be reduced. If the sensors prove especially reliable, they may even reduce the requirements for regular maintenance checks by engineers, perhaps making train tickets cheaper!
Edited by Frankie Macpherson
References
- Connolly, et. al. “Field testing and analysis of high speed rail vibrations”, Soil Dynamics and Earthquake Engineering, 67, 2014.
- https://interferencetechnology.com/electromagnetic-interference-sources-and-their-most-significant-effects
- Hwa Yaw-Tam, et. al. “Novel accelerometer realized by a polarization-maintaining photonic crystal fiber for railway monitoring applications”, Optics Express, 2019.
- https://www.rp-photonics.com/birefringence.html
- Hwa Yaw-Tam, et. al. “Novel accelerometer realized by a polarization-maintaining photonic crystal fiber for railway monitoring applications”, Optics Express, 2019.